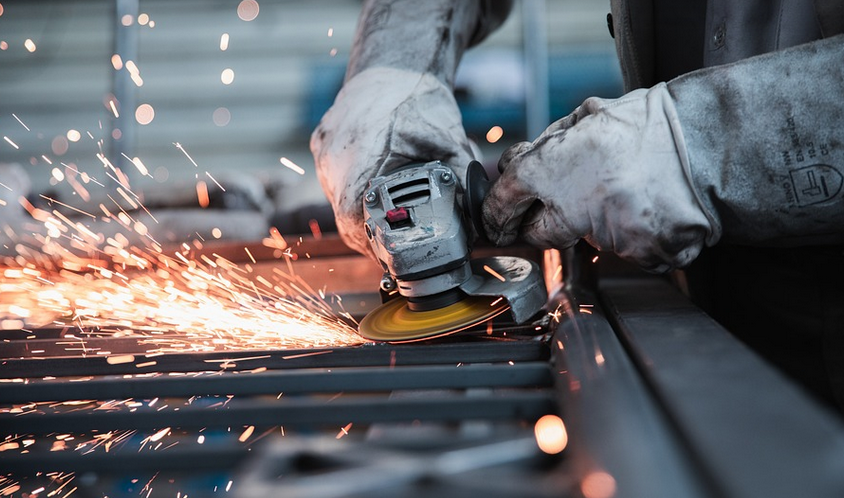
Replacement Rubber Tracks For Excavators: Keeping Your Construction Work Rolling
What are Rubber Tracks?
Rubber tracks, also known as rubber rollers or simply tracks, are a crucial component of many excavators and other heavy-duty machinery. They’re essentially rolling shoes made from durable rubber that provide the power to move heavy loads.
These rubber tracks offer significant advantages over conventional wheel systems. For one, they deliver superior traction on various terrains, allowing machines like excavators to navigate rough surfaces with ease. The unique design of the track makes it possible to tackle inclines and slopes with precision, making them a vital part of construction projects.
Rubber tracks also provide a smoother ride compared to wheels, leading to reduced vibrations caused by heavy machinery. This translates into less fatigue for operators and reduces wear and tear on other components of the excavator. Additionally, the rubber track system is remarkably flexible, allowing it to adapt to uneven terrain with relative ease.
But as with any component in a machine, especially one that experiences significant wear and tear over time, replacement tracks are an inevitable part of owning and operating an excavator.
Why Replace Rubber Tracks?
Replacing your rubber tracks might seem like an unnecessary expense, but it’s actually crucial for maintaining the efficiency and safety of your excavator. Regularly replacing rubber tracks is vital to ensure optimal performance and longevity.
When your rubber tracks are worn out, they can impact several aspects of your excavator’s operation.
**1) Reduced Track Life: ** Old or cracked tracks will wear down much faster, leading to a shorter lifespan for your machinery. This impacts productivity because you need replacement tracks sooner than expected.
**2) Decreased Traction and Stability:** Worn-out tracks impact the grip on various surfaces, leading to reduced traction and stability. You may experience difficulties maneuvering on uneven terrain or steep inclines.
**3) Increased Noise and Vibration:** Worn rubber can make a lot of noise and amplify vibration, which can be uncomfortable for the operator and potentially cause damage to surrounding structures.
**4) Fuel Efficiency Issues:** Worn tracks can lead to inefficient movement as the excavator will have to work harder to propel itself. This negatively impacts your fuel consumption.
**5) Increased Safety Risks:** Damaged tracks can compromise the stability and balance of your excavator, posing a safety risk to yourself and others.
Finding the Right Replacement Tracks for your Excavator
Replacing rubber tracks is not an easy process. You must choose the right replacement tracks based on various factors.
**1) Type of Excavator:** The size, make, and model of your excavator will determine which type of tracks are compatible with it.
**2) Load Capacity:** Think about the weight you need to move. Heavy-duty excavators require heavy-duty tracks that can withstand this load.
**3) Terrain Requirements:** If you work in a rough terrain, your track needs to be rugged enough to handle slopes, uneven ground and extreme weather conditions.
**4) Budget Constraints:** The cost of replacement tracks varies considerably depending on the brand and material used.
**5) Track Life Cycle:** How long do you intend to use these tracks before needing a full replacement? This will help you decide on a track type.
Once you have considered all these factors, you can start comparing different suppliers’ offerings and their quality, warranty guarantee, delivery time, and price.
**Pro-tip:** Don’t hesitate to talk to the manufacturer of your excavator about recommended replacement tracks. They will be able to provide specific advice for your machine.
The Importance of Professional Installation
Replacing rubber tracks is not a DIY job, it requires expert care and handling. The process involves several steps and expertise in track mounting and alignment.
**1) Safety Precautions:** The installation process requires special tools and equipment and can involve lifting heavy objects. Ensure you have the proper safety protocols and equipment before starting the project.
**2) Trained Technicians:** It’s best to leave the heavy lifting and track installation to a trained professional who has experience working with excavators.
**3) Track Balancing:** Incorrect track alignment can lead to uneven performance and potential wear, so it’s important to have a technician ensure proper balancing after installation.
**4) Quality Check:** The installed tracks should be checked for any damage or defects before the machine is put into service. This ensures the longevity of your excavator’s operation.
Maintenance Tips for Your Rubber Tracks
To extend the life and performance of your replacement rubber tracks, regular maintenance plays a significant role.
**1) Regular Cleaning:** After each job, clean the tracks to remove dirt, debris, and any accumulated dust.
**2) Lubrication:** Keep a look out for any signs of wear and tear on track components and have them lubricated as needed by a professional.
**3) Tire Pressure Check:** Check tire pressure regularly to ensure optimal performance and prevent uneven wear.
**4) Track Inspection:** Regularly inspect your tracks for any signs of damage or wear, such as cracks, tears, sharp edges, and excessive wear.
Following these tips and seeking regular professional maintenance can help you maximize the lifespan and efficiency of your excavator’s rubber tracks.
Conclusion
As with all critical machinery in construction, replacing your rubber tracks is a routine part of owning and operating an excavator. By taking care of your tracks, you can keep your work going smoothly, reduce downtime, and ensure maximum efficiency. Remember to consult the manufacturer’s guidance and consider investing in quality replacement rubber tracks for optimal performance.