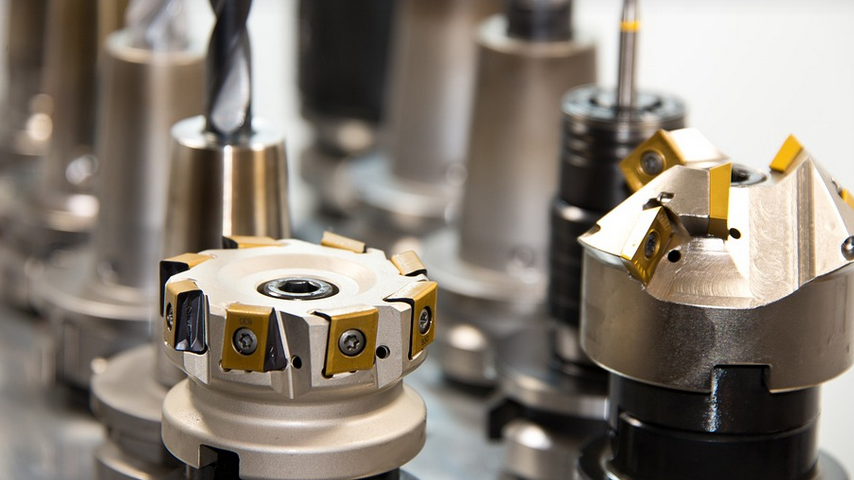
The Unsung Heroes Of Industry: Ir G Industrial Rubber & Gaskets
What are industrial rubber and gasket materials?
Industrial rubber and gaskets, often just referred to as “rubber,” play a crucial role in countless industries. These versatile products utilize specific types of rubber compounds and specialized manufacturing processes to create durable and reliable seals against harsh conditions.
Rubber, known for its elasticity and resilience, forms the backbone of industrial applications. It can withstand extreme temperatures and pressures while remaining flexible, making it ideal for sealing around moving parts, preventing leakage, and maintaining safe operation in various settings.
Gaskets are essentially rubber seals designed to create a tight, pressure-resistant seal between two mating surfaces. These can be simple O-rings or complex multi-layered designs used in intricate mechanisms. The precise size and shape of the gasket allow for controlled pressure build-up while preventing leaks and damage.
Industrial rubber & gaskets often utilize specific rubbers based on their intended use:
– **Natural Rubber (NR):** This versatile material is known for its elasticity, affordability, and resistance to abrasion. It’s a popular choice in general machinery and outdoor applications where durability and flexibility are key.
– **Synthetic Rubbers:** This category includes numerous rubbers like Butadiene Rubber (BR), Ethylene Propylene Diene Monomer (EPDM), Nitrile Butadiene Rubber (NBR), Silicone, etc. These offer even greater resistance to harsh chemicals, extreme temperatures, and challenging environments compared to natural rubber.
– **Specialty Rubbers:** Additional factors like chemical resistance, temperature extremes, or pressure requirements dictate the selection of specific rubbers. For example, Fluorocarbon Rubber (FKM) seals are used in demanding applications like high-pressure gas handling and automotive sealing where exceptional resistance to chemicals is critical.
Why Choose Ir G Industrial Rubber & Gaskets?
Industrial rubber and gaskets offer a range of benefits that make them essential elements in various industrial settings. Their key advantages include:
– **Durability:** These products are designed for long-lasting performance, withstand demanding mechanical stresses and vibrations, resist corrosion, and remain functional even under prolonged usage.
– **Reliable Sealing:** Their ability to create a tight seal ensures the prevention of leaks, maintaining system pressure, preventing environmental contamination, and reducing operational costs.
– **Temperature Tolerance:** Many rubber compounds can operate efficiently in diverse temperatures, from below freezing to high heat, ensuring consistent performance even under challenging conditions.
– **Chemical Resistance:** Several types of rubbers offer resistance against a wide range of chemicals, protecting sensitive equipment and settings from corrosion and degradation caused by various fluids or substances.
– **Cost-Effectiveness:** Rubber products are often manufactured with cost-efficiency in mind, enabling high-volume production and making them an economical solution for numerous industrial applications.
Where Can You Find Them?
Industrial rubber & gaskets are widely used across various industries. Let’s explore a few examples:
– **Manufacturing:** In factories, the use of gaskets ensures the safety and efficiency of machinery. From engine sealing to pipe connections, these products play an essential role in maintaining equipment functionality under heavy loads and challenging conditions.
– **Automotive:** Rubber components within vehicles are crucial for both performance and safety, including tires, seals, and hoses that prevent leakages while ensuring smooth movement of the vehicle.
– **Construction:** In construction, gaskets play a role in preventing leaks in pipes, water systems, and other critical areas. Their durability and resilience prove vital in demanding weather conditions and varying environmental factors.
– **Power Generation:** Rubber & gasket materials are indispensable in power generation facilities for high-pressure steam and gas handling systems, ensuring safe and efficient operation within potentially explosive environments.
Choosing the Right Material: Key Considerations
Selecting the right rubber and gasket material requires careful consideration of various factors. The specific application will dictate which type of material is best suited for its intended purpose:
– **Operating Temperature:** Determine if the product will be exposed to extreme heat or cold, as this can affect the performance of different rubbers.
– **Pressure and Load:** Evaluate the maximum pressure and loads expected in the system. This information helps determine the required strength and flexibility of the rubber components.
– **Chemical Environment:** Analyze the potential presence of chemicals or fluids that may interact with the gasket material, as this will influence its longevity and performance.
– **Durability Requirements:** Assess the product’s intended lifespan and operating environment to ensure the chosen material can withstand the anticipated stresses and strains for extended periods.
– **Cost-Effectiveness:** Determine your budget constraints while balancing performance requirements. Comparing different rubber types and suppliers will help you find the most cost-effective solution.
How to Maintain Your Gaskets
To maximize the lifespan and performance of your industrial rubber & gaskets, consider these maintenance tips:
– **Regular Inspection:** Schedule periodic inspections for signs of wear and tear. Checking for cracks, damage, or any potential leakage points will help prevent premature failures.
– **Proper Cleaning:** Ensure all surfaces are clean and free from debris before sealing to avoid contamination that may affect the gasket’s performance.
– **Lubrication:** Apply lubricant to moving parts as needed to reduce friction and extend the life of your gaskets. This can ensure smooth operation and prevent unnecessary wear.
– **Storage and Handling:** Store rubbers in a cool, dry place away from direct sunlight or heat sources to prevent degradation and premature deterioration over time. Handle them carefully during installation and maintenance to avoid damage.
By implementing these measures, you can ensure optimal performance of your industrial rubber & gaskets and extend their lifespan throughout the product’s entire lifecycle.